Надежность КрАЗ
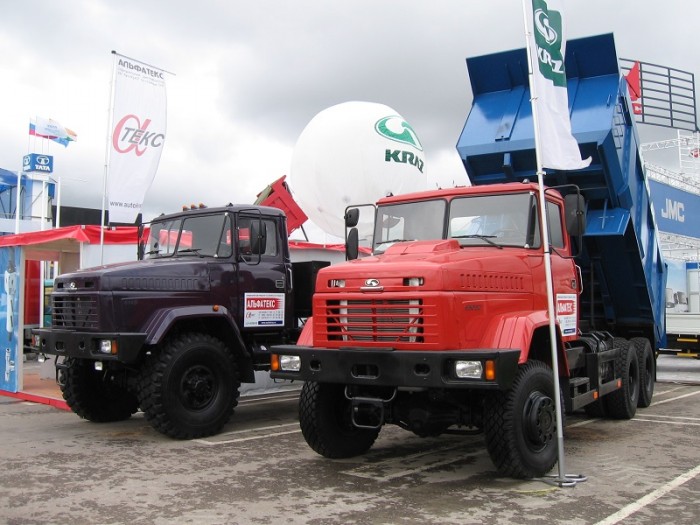
Надежность автомобиля КрАЗ непосредственно зависит от совершенства технологического процесса и качества изготовления его деталей. На заводе КрАЗ проведен ряд технологических мероприятий по увеличению надежности выпускаемых автомобилей, охвативших все виды производства: сварочное производство, механическую обработку, нанесение гальванопокрытий, сборку автомобилей и т. д.
Уровень механизации сварочных работ доведен до 81,95%. Перевод с ручной сварки на полуавтоматическую в среде углекислого газа балансиров задней подвески исключил брак по сварке этой детали. Высокое качество сварного соединения реактивной штанги и шаровых опор обеспечивается автоматической сваркой, рычагов управления - сваркой трением и т. п. С 1968 г. на изготовление методом холодного выдавливания и методом высадки с электронагревом переведено девять деталей. Вследствие применения этих прогрессивных методов завод получил существенный экономический эффект при одновременном уменьшении расхода металла и улучшении качества деталей.
На заводе КрАЗ широко применяется внедренный при помощи института НИИТавтопром метод поверхностного пластического деформирования, позволяющий увеличить износостойкость деталей вследствие получения более чистой поверхности и повысить их прочность благодаря образованию наклепанного слоя. Насколько эффективен этот метод, свидетельствуют следующие данные. Внедрение раскатывания отверстий бронзовых втулок раздаточной коробки позволило увеличить их долговечность на 10%.
Обкатывание шеек фланцев карданных валов улучшило работоспособность сальников. Раскатывание внутренней поверхности тормозных барабанов дало возможность повысить их долговечность на 15%. В настоящее время методом поверхностного пластического деформирования обрабатывается 53 детали: шейки промежуточного вала раздаточной коробки и фланцев карданных валов; шток амортизатора сиденья; поверхность трения тормозного барабана; сфера сателлита; торец и сфера чашки дифференциала; шейки оси балансирной подвески; зев полуосей переднего моста; сфера и галтели шаровых опор и др.
Системы управления качеством на автозаводах
Коллективы Ярославского моторного завода и Кременчугского автомобильного завода внедрили системы управления качеством, учитывающие специфику производства дизельных силовых агрегатов и автомобилей. Эффективность этих систем подтверждена признанием успеха обоих предприятий в повышении надежности автомобилей КрАЗ и дизелей ЯМЗ. Опыт двух передовых предприятий свидетельствует о необходимости применения систем управления качеством на следующих стадиях создания и эксплуатации автомобилей:
- отработки новых объектов с более высоким планируемым уровнем ресурса, чем у ранее освоенных конструкций; на данной стадии осуществляются конструкторская разработка и экспериментальные исследования объектов производства, а также разработка технологических решений, связанных с обеспечением заданных параметров;
- подготовки производства нового изделия;
- освоения производства изделия и его эксплуатации с доработкой конструкции и технологии, необходимой для достижения заданного уровня параметров, по результатам экспериментальных работ и изучения опыта эксплуатации крупных партий автомобилей;
- последующего систематического повышения уровня надежности и равностойкости конструкции по данным экспериментальных работ и всестороннего изучения опыта эксплуатации.
Системы управления качеством развиваются по мере накопления опыта работ, связанных с совершенствованием изделия на перечисленных выше стадиях.
Автомобиль в условиях массовой эксплуатации при систематическом проведении технического обслуживания на основании теории надежности можно рассматривать как систему с периодическим техническим обслуживанием. Среди разновидностей этих систем автомобильной технике наиболее соответствуют восстанавливаемые системы (что достигается в результате технического обслуживания и ремонта) многоразового применения. Математический аппарат анализа надежности подобных систем основан на теории вероятностей, в том числе теории информации и теории массового обслуживания.
Из задач вероятностного анализа эксплуатационной информации, помимо установления статистических показателей надежности, следует назвать определение вероятностного гамма-процентного ресурса, выявление вероятного числа отказов на единицу наработки, установление законов распределения отказов. Определение соответствующего закона для узла или детали способствует выработке гипотезы выхода их из строя, что упрощает планирование работ по повышению надежности. Весьма важной является возможность использования вероятного закона распределения для прогнозирования надежности при ограниченных данных о наработке изделий за обследуемый период.
Методика применения теории надежности сложных систем всесторонне разработана, и распространение этой теории на автомобили и их агрегаты способствует укреплению теоретического базиса работ по повышению надежности и дает возможность наметить путь их развития. Напомним, что повышение надежности изделий в процессе их серийного и тем более массового производства является естественным процессом, охватываемым понятием конструкторской и технологической доработки.
Принципиально возможна конструкторская отработка системы лишь путем предварительной отработки ее элементов по надежности, однако на основании теории и практики установлена предпочтительность сочетания предварительной отработки отдельных элементов и комплексной отработки их в составе системы (в данном случае автомобиля) в тех случаях, когда имеется взаимосвязь надежности составных частей конструкции. Такая взаимосвязь характерна как для автомобиля в целом, так и для силового агрегата.
Улучшение качества и увеличения сроков службы лакокрасочных покрытий
Для улучшения качества и увеличения сроков службы лакокрасочных покрытий широко применяются новые процессы окраски, а также новые эмали, краски, грунты. Разработан и внедрен новый комплексный процесс окраски кабин и топливных баков с заменой щелочного обезжиривания на фосфатирование и с применением водорастворимого грунта ПФ-ОЗЗП и меламино-алкидных эмалей МЛ-12. Это мероприятие позволило увеличить срок службы лакокрасочных покрытий на узлах кабины и оперения с одного года до 4 лет. Окраска бортов и каркасов кабин эмалями МЧ-145 вместо эмали ЗИС увеличила срок службы покрытий с одного года до 2 лет. Внедрена окраска узлов и деталей шасси эмалью МЧ-123. Осваиваются также новые методы химико-термической и термической обработки деталей.
В 1968 г. ряд ответственных шестерен редуктора был переведен на обработку в безмуфельном автоматизированном агрегате типа СТЦЛ с автоматически регулируемым углеродным потенциалом. Обработка шестерен по новой технологии позволила получить заданную оптимальную концентрацию углерода в цементованном слое (0,85-0,95%), повысить твердость поверхности зубьев, уменьшить деформацию шестерен, вследствие чего увеличился ресурс редуктора автомобиля. К началу 1972 г. цементация 87% деталей производилась в безмуфельных агрегатах.
Работниками отдела главного металлурга были разработаны и внедрены процессы безокислительного нагрева ряда улучшаемых деталей в комплексно-механизированных закалочно-отпускных агрегатах типа СКЗ и СТЗ. Внедрение защитной атмосферы типа эндогаз и экзогаз в закалочных и отпускных печах позволило устранить на поверхности изделий (стремянки, валы, шаровой палец, резьбовые нормали) обезуглсроженный слой, окалину и, как следствие, повысить их усталостную прочность.
На заводе внедрены новые методы гальванопокрытий, такие, как фосфатирование деталей шарниров переднего моста с последующей пропиткой дисульфидом молибдена, о чем упоминалось ранее, твердое хромирование деталей гидроусилителя рулевого управления и т. д.