Надежность дизелей
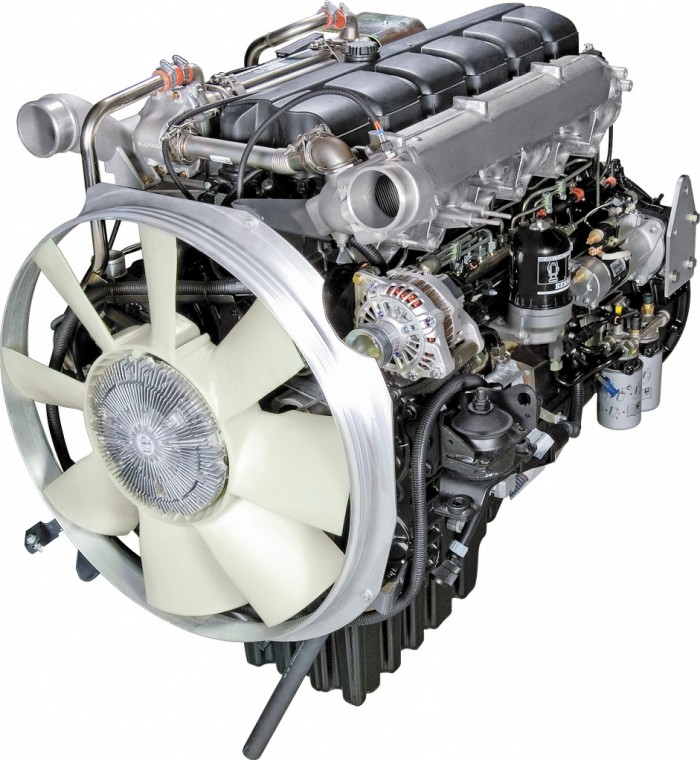
Важнейшей составной частью комплексных систем управления качеством являются исследования как на предпроектных стадиях, так и на стадиях конструкторской отработки, доработки и последующего совершенствования конструкции. Развитие исследований, являющееся характерной чертой современных систем управления качеством, приобретает все большее значение в условиях научно-технической революции.
Исследования, имеющие своей целью оценку и повышение надежности, могут быть условно разделены на лабораторные и эксплуатационные.
Лабораторные исследования - основное средство отработки изделий по надежности прежде всего на стадии конструкторских работ.
Технический прогресс невозможен без сокращения сроков создания машин и их конструкторской доработки по надежности. В связи с этим объем лабораторных исследований прогрессивно возрастает, а их методологический уровень повышается. Этим объясняется большое внимание, уделяемое коллективами ЯМЗ и КрАЗ развитию лабораторной базы.
Эксплуатация является основной сферой, где выявляется надежность автомобиля, поэтому одновременно с развитием лабораторных исследовательских работ по надежности коллективы обоих предприятий стремятся к максимальному расширению и углублению эксплуатационных исследований.
Кроме состояния лабораторной базы, результативность исследований обоих видов в значительной степени зависит от совершенства применяемых методик.
Вследствие увеличения объема и интенсификации исследований в число их участников вовлекаются работники различных сфер: отработки объектов, производства, изготовления материалов и комплектующих изделий, а также эксплуатации. Это является одной из характерных черт системы работ по повышению надежности, проводимых ЯМЗ и КрАЗ.
Отработку изделий по надежности целесообразно осуществлять с использованием методов статистических исследований, проведение которых только в лабораторных условиях при неизмеримо большом количестве сочетаний факторов, характеризующих условия эксплуатации машин (автомобилей), оказывается недостаточным. Поэтому коллективы ЯМЗ и КрАЗ придают важнейшее значение организации и совершенствованию методики эксплуатационных исследований.
Оценка надежности дизелей
Оценка надежности по результатам локальной эксплуатации небольших партий автомобилей в характерных "эталонированных" условиях целесообразна для выявления изменения качества агрегатов в зависимости от их возраста или по сериям выпуска.
Число объектов, проходящих эксплуатационную стадию первичной доводки автомобилей КрАЗ и дизелей ЯМЗ, систематически растет. В начале 50-х годов оно составляло 3-5 образцов, а в начале 60-х годов возросло до 20-30 образцов. В настоящее время признано целесообразным увеличение опытных партий силовых агрегатов, проходящих проверку в условиях эксплуатации до начала массового или крупносерийного производства, до 100-200 шт., что и реализуется ЯМЗ. Это позволяет достаточно полно использовать методы математической статистики для оценки надежности изделий. Нетрудно прогнозировать дальнейший рост партий автомобилей и силовых агрегатов, проходящих лабораторно-эксплуатационные испытания, по мере сокращения срока морального старения и повышения стоимости подготовки автоматического и автоматизированного производства. В этой связи очевидна необходимость наряду с дальнейшим развитием экспериментальных цехов создания цехов опытных серий.
Надежность, в особенности безотказность автомобилей и их агрегатов, изготовляемых методами массового производства, зависит помимо других факторов от многих производственных факторов и тесно связана с однородностью качества изготовления изделия. Ниже эти вопросы рассмотрены более подробно для основной продукции заводов ЯМЗ и КрАЗ. Напомним, что систематические заводские испытания автомобилей и двигателей серийного производства позволяют получить выборочные данные об их надежности в условиях ограниченной транспортной работы и изменении качества продукции по годам выпуска, хотя это лишь в ограниченной мере характеризует эксплуатационную надежность изделий.
Возвращаясь к вопросам экспериментальной доработки автомобилей и их агрегатов, отметим, что увеличение объема необходимой эксплуатационной информации, связанное со стремлением сократить время доработки образцов, определяет целесообразность совершенствования системы эксплуатационных испытаний, служащей естественным дополнением к другим, ранее освоенным формам связи заводов - изготовителей двигателей и автомобилей с эксплуатирующими организациями.
Целью этой связи является в первую очередь получение максимально достоверной информации о качестве продукции, выпускаемой заводом-изготовителем. Большое значение имеет и другая положительная сторона указанной связи - активное воздействие завода-изготовителя па эффективность использования технико-экономических возможностей изделия, а следовательно, и на повышение производительности труда при его эксплуатации.
Сохраняют свое значение и такие формы получения информации, как разовые, локальные и региональные обследования автомобильных хозяйств, инструктивные выезды представителей заводов в них, метод опроса, традиционные заводские конференции по качеству продукции, а также наличие постоянных корреспондентов. Контингент последних подбирают представители заводов при разовых обследованиях, инструктаже и других контактах с организациями, получающими крупные партии новых автомобилей. Существенное значение имеет взаимная информация кооперируемых предприятий.
Использование перечисленных выше форм связи сфер производства и эксплуатации позволило систематически увеличивать поток информации о качестве продукции, выпускаемой автомобильным и моторным заводами, и на этой основе повысить достоверность статистической информации о надежности дизелей ЯМЗ и автомобилей КрАЗ с дифференциацией ее по характеру условий эксплуатации, что весьма желательно для разработки конструктивных и технологических мероприятий по повышению надежности (ресурса) данных объектов.
Однако качество информации подобного рода оказалось недостаточным для эффективного развития поисковых работ по повышению надежности, поскольку эта информация не всегда отражает закономерности рабочих процессов механизма, а также многообразие производственных факторов. Вследствие этого, продолжая использовать ранее сложившиеся связи и совершенствовать их, вводя, например, опросные формы с двоичной системой заполнения, пригодные для обработки с применением ЭВМ, Ярославский моторный завод в 1963-1964 гг. начал поиски новой формы информационной связи со сферой эксплуатации. Оказалось целесообразной организация системы базовых автотранспортных хозяйств (БАТХ) с различными категориями условий эксплуатации автомобилей.
Расчет показателей надежности дизелей
Важнейшим этапом обработки информации по надежности является математико-статистический расчет ее показателей, основанный на вероятностных методах.
Математико-статистический расчет, основанный на вероятностном методе, позволяет определить:
средний и гамма-процентный ресурс деталей до первой замены и между заменами;
средний и гамма-процентный ресурс узлов до первой замены или до ремонта определенного вида;
средний и гамма-процентный ресурс агрегатов (двигателя, коробки передач и т. п.) до первого капитального ремонта и между капитальными ремонтами.
Другими показателями надежности, определяемыми также с помощью методов математической статистики, являются: вероятность безотказной работы, наработка до отказа, интенсивность и поток отказов по определенной детали, узлу, агрегату.
Для определения уровня ремонтной технологичности изделия, а также совершенства технологии ремонта, применяемой па ремонтных предприятиях, производят оценку надежности изделий, прошедших капитальный ремонт на специализированном ремонтном предприятии. Подконтрольную партию для такой оценки подбирают специально.
Таким образом, расчет показателей надежности изделий ЯМЗ, как в принципе и других узлов автомобилей КрАЗ, производится раздельно по деталям, узлам и агрегатам.
Учетные документы для сбора информации по надежности дизелей
К основным учетным документам для сбора информации по изделиям ЯМЗ относятся: акт осмотра дизеля перед вводом его в эксплуатацию, карта ремонта изделия, карта учета эксплуатации изделия и карта учета расхода запасных частей, в которую записываются все детали, отпускаемые для ремонта каждого из объектов подконтрольной партии.
Карта ремонта узла, агрегата или изделия ЯМЗ, заполняемая механиком во время их ремонта, является первичным документом, в котором записывается внешний признак, послуживший причиной постановки изделия в ремонт, возможная причина отказа, а также перечень и техническое состояние всех замененных деталей.
Исследование причин, вызвавших ремонт изделия, и предположительное указание детали, техническое состояние которой обусловило необходимость ремонта изделия, производит лицо, ответственное за техническую информацию, совместно с работниками БАТХ.
Карту учета эксплуатации изделия ведет работник, ответственный за техническую информацию, совместно с персоналом технических служб БАТХ с начала ввода подконтрольного объекта в эксплуатацию до сдачи его на ремонтный завод. Эта карта является документом, в котором концентрируются все технико-экономические показатели работы изделия: объем выполненной автомобилем транспортной работы, наработка двигателя за отчетный период и с начала эксплуатации, расход топлива и угар масла, давление масла в двигателе, количество проведенных ТО-1 и ТО-2.
Сведения, содержащиеся в первичных учетных документах, составляют необходимую для завода информацию, которую ответственный за нее переносит в информационные карты. Эти карты на заводе обрабатываются на ЭВМ, поэтому всю информацию кодируют по соответствующим классификаторам шифров, приведенным в инструкции по сбору информации. Составление и оформление информации и направление ее на завод является завершающим этапом работ по ее сбору, при этом карты-носители, акты и протоколы, включая протоколы технического совета предприятия, дополняются эскизами, фотографиями, экземплярами отказавших деталей и узлов, микрометражными картами.
Работники службы надежности ЯМЗ, кроме получения непрерывной периодической информации, позволяющей определять уровень эксплуатационной надежности выпускаемой заводом продукции, выполняют в БАТХ большую исследовательскую работу по определению природы возникновения отказов, проводят испытания опытных образцов деталей, узлов и изделий в целом, сочетая выполнение работ по специальным программам с проверкой качества и полноты ведения учетной документации.
Работа с БАТХ
Опыт работы с БАТХ показал преимущества этой формы сбора информации по сравнению с другими видами. Положительным является высокая достоверность результатов при достаточном для статистического анализа размере выборок, совокупность которых отражает результаты эксплуатации автомобилей в масштабе страны; оперативность связи и возможность контроля за достоверностью результатов но специальным программам; получение информации в кодированной форме, удобной для обработки с помощью ЭВМ; оперативность передачи отказавших деталей изделия на завод-изготовитель для исследования; возможность выявления корреляционных связей результатов стендовых и эксплуатационных испытаний.
Последнее обусловлено возможностью использования БАТХ для активных поисков информации.
В настоящее время большинство БАТХ являются общими для объединения "Автодизель" и КрАЗ, что позволяет комплексно производить анализ надежности всех элементов автомобиля, определять взаимосвязь отказов и разрабатывать совместные мероприятия по их устранению. Вследствие общности исследовательской базы объединения "Автодизеля" и КрАЗ стала возможной организация системы сбора информации, обеспечивающей комплексность и достоверность последней.
Следует отметить, что указанные положительные стороны системы получения информации о надежности с помощью БАТХ в полной мере выявились при усложнении задач, поставленных перед заводами-изготовителями по повышению качества продукции и нормируемого ресурса в связи с его ростом.
Вследствие увеличения планируемого срока службы автомобилей стал необходим учет факторов, связанных со старением, ползучестью и другими, относительно медленно развивающимися явлениями, возможность изучения которых в процессе стендовых испытаний ограничивается чрезмерной длительностью соответствующих программ.
Таким образом, введение системы БАТХ улучшило связь производства и автотранспортных предприятий. Очевидно, что комплексная система связи, не является окончательной. Предполагается внедрение фирменной системы капитального ремонта. Не исключена целесообразность распространения на автомобили большой грузоподъемности и системы фирменного технического обслуживания.
Наряду с комплексом БАТХ развивается и получает все более широкое признание система экспериментально-производственных автомобильных хозяйств (ЭПАХ) Центрального научно-исследовательского автомобильного и автомоторного института (НАМИ), обеспечивающая максимальную объективность информации. В результате объем и достоверность информации о качестве и, в частности, о надежности автомобилей большой грузоподъемности возрастают еще больше.
Статистическая информация о надежности дизелей
Информация о надежности имеет особенности, которые определяют предъявляемые к ней требования. Эта информация должна быть:
полной настолько, чтобы обеспечить решение задач, возникающих при разработке новых изделий, а также при повышении-надежности и улучшении условий эксплуатации ранее освоенных изделий;
достоверной, т. е. отражающей действительные события, и подкрепленной фактическими данными по характеру отказов, величине износа, состоянию рабочих поверхностей деталей или сопряжений;
оперативной и непрерывной по связи с заводом-изготовителем;
в необходимой мере дискретной, т. е. сообщения должны быть разделены по отдельным признакам.
Система получения информации о надежности изделий массового производства в условиях эксплуатации должна обеспечивать достоверность оценки данного качества изделия. Информация о надежности в сфере эксплуатации прежде всего должна содержать сведения об отказах, каждый из которых является следствием совокупности производственных (включая конструктивные) или эксплуатационных факторов. Поэтому поток информации следует организовать так, чтобы она содержала первичные гипотезы причин отказов или, при невозможности этого, классификацию возможных причин отказов по их вероятности.
Сложность классификации отказов повышается по мере старения парка объектов вследствие износа деталей, отклонений их сопряжений от оптимального состояния, развития процессов усталости, релаксации внутренних напряжений, проявления ползучести, эррозин, коррозии и т. п. Вследствие этого при выработке первичных гипотез причины отказов должно учитываться сокращение остаточного ресурса изделий по мере увеличения наработки и старения парка автомобилей.
Последовательность обработки информации о надежности дизелей
Обработка поступившей на завод информации, содержащей сведения о техническом состоянии и отказах подконтрольных изделий, состоит из следующих этапов:
- контроль и подготовка информации для передачи ее в вычислительный центр завода;
- создание машинных носителей информации;
- обработка на ПК.
Первый этап обработки информации выполняется в эксплуатационно-исследовательском бюро отдела главного конструктора и включает:
проверку полноты и правильности заполнения граф информационных карт, а также соответствие цифровой и текстовой частей информации по классификаторам шифров;
подготовку информации для передачи в вычислительный центр завода, в процессе которой информационные карты формируются в поток. Каждая пачка сшивается и снабжается специальным сопроводительным талоном.
Дальнейшая обработка информации производится в вычислительном центре. Исходные данные для машинной обработки можно разделить па переменные и постоянные. К переменным данным относятся сведения, содержащиеся в информационных картах о техническом состоянии и отказах подконтрольных изделий; к постоянным относятся следующие: заводской номер дизелей, марка модели и год выпуска, дешифратор наименовании деталей и узлов изделия, а также оптовые цены запасных частей, дешифратор характера отказов деталей и узлов изделия; нормативы трудоемкости технического обслуживания (ТО) и стоимость работ, включенных в ТО. Постоянная информация подлежит периодической проверке и корректировке.
Второй этап обработки - создание машинных носителей информации-перфокарт и магнитных лент. Для этого всю информацию, содержащуюся в информационных картах, делят па четыре части, отражающие следующее:
- техническое состояние подконтрольного изделия;
- характеристику отказов агрегатов и систем изделия, вид и место его ремонта;
- номенклатуру замененных и восстановленных деталей (узлов) с указанием характера и места отказа;
- трудозатраты по устранению отказов и ТО изделия.
Такое деление информации позволило создать четыре вида машинных носителей - четыре макета перфокарт, что дает возможность получить необходимые выборки без обработки всей информации, заключенной в информационных картах:
- макет № 1 отражает техническое состояние изделия, не имевшего отказов в течение отчетного периода;
- макет № 2 включает информацию по техническому состоянию и характеру ремонта изделия, имевшего в течение отчетного периода отказы и неисправности;
- макет № 3 содержит информацию о деталях (узлах), замененных или восстановленных при ремонте изделий в эксплуатирующей организации, с определением характера, координат, способа устранения отказа, количестве одновременно отказавших деталей одного наименования, а также отмечается вероятность того, что отказ изделия был вызван несовершенством функционирования данной детали (далее употребляется сокращенный термин "вероятность причины");
- макет № 4 включает информацию о выполненной изделием в течение отчетного периода работе, расходе эксплуатационных материалов, трудозатратах и стоимости работ по устранению отказов в эксплуатирующих организациях.
Третий этап - обработка информации на ЭВМ с целью создания накопителей информации. При этом возможна как раздельная, так и совместная обработка информации, содержащейся в машинных носителях. Обработка информации на этом этапе производится в следующем порядке: ввод информации с перфокарт в ЭВМ, формирование информационных массивов на магнитной ленте, сортировка и создание упорядоченных массивов, расчет и вывод на печать ведомостей-накопителей.
В настоящее время объем накапливаемой информации позволяет создавать три информационных массива.
- Массив № 1, содержащий информацию перфокарт но макетам № 1 и 2, служит для выдачи сводки № 1 "Техническое состояние изделия" но каждому из подконтрольных объектов наблюдения (форма 1).
- Массив № 2, включающий в себя информацию, которая имеется в перфокарте по макету № 3, служит для выдачи следующих ведомостей-накопителей (сводок):
- "Детали (узлы), замененные или восстановленные при эксплуатации изделия" - сводка № 2 (форма 2), которая так же, как и сводка № 1, выдается по каждому из подконтрольных изделий;
- "Характеристика неисправностей детали (узла)" - сводка № 3 (форма 3), которая выдается по основным деталям, исключая нормализованные;
- "Расход запасных частей" - сводка № 4 (форма 4), отражающая расход запасных частей за различные периоды эксплуатации (год, несколько лет и т. д.) по подконтрольным изделиям одного или разных годов выпуска, эксплуатирующихся в одной организации.
- Массив № 3, содержащий информацию перфокарты по макету № 4, служит для выдачи ведомости-накопителя "Затраты на техническое содержание изделия" - сводка Л" 5, которую составляют по каждому из подконтрольных изделий.
Таким образом, в результате обработки эксплуатационной информации на ЭВМ получают ведомости - накопители информации, необходимые для дальнейшего анализа результатов эксплуатации изделий ЯМЗ в различных условиях, а также для оценки "представительности выборки" перед выполнением вероятностного расчета показателей надежности отдельных деталей, узлов и изделия в целом.
После создания перфокарт проверяют отпечатанные сводки № 1-5 чтобы выявить ошибки, допущенные при вводе информации на ЭВМ (утеря перфокарт) или первичном контроле. Кроме того, может обнаружиться, что нарушена периодичность поступления информации по отдельным подконтрольным изделиям и другие обстоятельства, которые потребуют дополнительного выяснения в эксплуатирующих организациях. Поэтому с целью устранения ошибок при вводе дополнительной информации предусматривается корректировка информационных массивов № 1-3. Для проведения такой корректировки выдается специальное "извещение" об изменении соответствующего информационного массива. В случае корректировки обработка информации повторяется, но выдача документов производится только по тем номерам изделий, которые были включены в извещение об изменении.
Процесс формирования статистических рядов
Одним из этапов определения показателей надежности является процесс формирования статистических рядов, необходимых для дальнейшего математико-статистического расчета. В настоящее время формирование статистических рядов осуществляется путем логического анализа ведомостей-накопителей ннформации сводок №№ 1 и 3. Данные, необходимые для расчета показателей надежности агрегатов, включены в сводку № 1, данные же для расчета подетальной и поузловой надежности определяют при совместном анализе сводок № 1 и 3. В дальнейшем формирование статистических рядов по агрегатам, узлам и деталям предполагается проводить путем машинного анализа систематизированной информации.
В процессе формирования статистических рядов по отказам деталей, узлов и агрегатов возможны следующие варианты выборок (ГОСТ 17509-72 и ГОСТ 17510-72):
- Полная выборка;
- Усеченная выборка.
В обоих из этих планов производится усечение или но проценту отказов г от числа объектов, поставленных под наблюдение, или по времени, в течение которого ведутся эти наблюдения. Возникает ситуация, имеющая характер незавершенных испытаний с отказами и приостановлениями. Приостановленными считаются изделия, которые в момент оценки не имели отказа данного вида. Задача в этом случае заключается в прогнозировании отказов при завершении испытаний.
После формирования статистических рядов по деталям, узлам, агрегатам производится математико-статистическая обработка информации, основанная на вероятностном методе, который позволяет выявить закономерность распределения отказов анализируемых объектов.
Варианты выборок
На практике при оценке различных деталей или узлов силовых агрегатов используют оба варианта выборок. Однако наиболее часто продукцию оценивают по усеченной выборке, чтобы не ждать конца испытаний, т. е. момента, когда все подконтрольные изделия откажут, или момента, когда все неотказавшие изделия будут иметь определенную наработку.
Данный метод, построенный на вероятностной основе, позволяет после определения соответствия, эмпирического статистического ряда одному из теоретических законов распределения прогнозировать показатели надежности изделия, т. е. оперативно и с достаточной точностью оценивать надежность любой партии изделий через 2-2,5 года после ввода их в эксплуатацию, не дожидаясь, пока все они будут иметь отказы рассматриваемого вида. Так как надежность силовых агрегатов относительно высока, установить ресурс большинства деталей и узлов каким-либо другим методом до освоения модернизированной модели затруднительно.
Усеченную выборку используют в том случае, когда отказы какой-либо детали или узла изделия происходили не менее чем на 40% объектов подконтрольной партии. Однако этот метод можно использовать и при меньшем проценте отказов, но в этом случае оценку следует считать предположительной.
Математико-статистические исследования можно выполнять графо-аналитическим и аналитическим способами.
При графоаналитическом способе закономерность распределения отказов определяется путем нанесения на вероятностные бумаги значений накопленных частот для каждого из интервалов эмпирического ряда распределения отказов. Соответствие эмпирического распределения тому или иному теоретическому определяют по критерию согласия Пирсона, характеризующего расхождение между теоретическим и статистическим распределениями. При определении накопленных частот для каждого из интервалов статистического распределения отказов используют формулы математической статистики. Определение порядка распределения отказов при усеченной выборке основано на методе незавершенных испытаний. Следует отметить, что графо-аналитический способ не обеспечивает достаточной точности из-за погрешности графического определения параметров теоретических распределений.
Аналитический способ
Наибольшую достоверность результатов дает аналитический способ, при котором параметры теоретического распределения рассчитывают по аналитическим зависимостям. Однако этот способ из-за сложности и трудоемкости расчетов может быть применен только при использовании ЭВМ. Алгоритмы и программа для расчета показателей надежности на ЭВМ "Минск-22" разработаны на Горьковском автомобильном заводе.Расчет показателей надежности изделий ЯМЗ по автокодовым программам для этой машины показал, что данный способ не только приемлем, но и позволяет значительно сократить время, затрачиваемое на обработку эксплуатационной информации. Поэтому в настоящее время именно этот способ расчета показателей надежности применяется на ЯМЗ.
После математико-статистической обработки информации на ЭВМ результаты выдаются в виде специальных сводок, представляющих собой решение задачи. Эти сводки выдаются с проверкой соответствия эмпирического закона распределения трем теоретическим законам распределения отказов: нормальному, логарифмически-нормальному и Вейбулла.
Основные направления исследований дизелей
Исследование надежности. Вопросы исследования и определения уровня надежности изделий решаются эффективней и проще, если детали и узлы исследуемых объектов условно объединить в группы с близкой долговечностью. Критериями для объединения деталей и узлов в группы являются:
- уровень долговечности, который планируется в зависимости от назначения, сложности и стоимости элементов конструкции с учетом их функциональной связи;
- уровень трудоемкости замены детали или устранения ее отказа.
Проведенные исследования определили целесообразность объединения детален и узлов изделий ЯМЗ в три основные группы, которые отличаются между собой как диапазоном долговечности, так и трудоемкостью устранения отказа.
Первая группа - детали и узлы, долговечность которых больше или равна долговечности изделия до списания. Отказы деталей данной группы требуют для своего устранения полной разборки изделия, т. е. характеризуются максимальной трудоемкостью устранения неисправности, и являются одним из критериев необходимости проведения капитального ремонта изделия. Все детали данной группы ремонтируемые, т. е. при капитальном ремонте изделия их допускается восстанавливать путем шлифовки, притирки, расточки и т. п. Уровень надежности деталей и узлов этой группы оценивается параметрами долговечности до ремонта и безотказности до замены. К этой группе относятся базовые и основные детали изделия: блок цилиндров, коленчатый и распределительный валы, головки блока, картер маховика, шатун и др.
Вторая группа - детали и узлы, долговечность которых меньше долговечности изделия до списания, но больше или равна его долговечности до первого капитального ремонта. Замена деталей данной группы осуществляется, как правило, не ранее первого капитального ремонта изделия. Уровень надежности деталей и узлов данной группы оценивается параметрами долговечности и безотказности. К этой группе деталей и узлов относят в большинстве случаев поршни, гильзы, подшипники распределительного вала, детали механизма газораспределения, сальниковые уплотнения коленчатого вала и др.
Третья группа - детали и узлы, вероятная долговечность которых ниже долговечности изделия до первого капитального ремонта. При достижении изделием определенной наработки детали и узлы этой группы допускается в соответствии с рекомендациями завода-изготовителя или по признаку неудовлетворительной их работы заменять или ремонтировать, чтобы поддержать заданный уровень надежности и ресурса изделия.в целом. Надежность деталей и узлов этой группы оценивается как параметрами безотказности, так и параметрами долговечности. К числу деталей этой группы относятся: поршневые кольца, вкладыши коренных и шатунных подшипников коленчатого вала, прокладки головок блока, детали уплотнения водяного насоса, распылители форсунок и др.
Для замены деталей второй и третьей групп требуется частичная разборка изделия. Работы по устранению отказов могут производиться непосредственно на автомобиле (без снятия с двигателя) и, следовательно, характеризуются значительно меньшей трудоемкостью по сравнению с трудоемкостью замены или восстановления деталей первой группы.
Этапы исследований надежности дизелей
Первым этапом исследования надежности изделий и деталей каждой из групп является определение количественных показателей их долговечности, безотказности и ремонтопригодности, расчет которых базируется на использовании основных положений теории вероятностей и математической статистики. По полученным показателям оценивают уровень фактической надежности изделия относительно заданных нормативов, а также сопоставляют уровни надежности деталей внутри каждой из групп. Результаты этого этапа - основа для более глубокого анализа результатов эксплуатации изделия в реальных условиях.
Дальнейшее исследование ведется в двух направлениях:
- определение уровня долговечности и безотказности изделий но годам выпуска в идентичных условиях эксплуатации;
- совместный анализ уровня надежности изделий и условий их эксплуатации для определения влияния отдельных эксплуатационных факторов или их комплекса на надежность выпускаемой заводом продукции.
К основным эксплуатационным факторам относятся климатические и дорожные условия, скоростные и нагрузочные режимы, тепловой режим работы и его стабильность, применяемые топливно-смазочные материалы и охлаждающие жидкости, число циклов включения (выключения) передач, относительное время или частота использования передач в коробке передач, система, периодичность и уровень технического обслуживания, а также качество ремонта. Учет этих факторов требует проведения в эксплуатирующих организациях специальных исследовании, что и осуществляется работниками эксплуатационно-исследовательского бюро в соответствии с разработанными для этого программами.
Исследования по выявлению комплекса показателей долговечности и безотказности позволяют:
- оценить эффективность внедренных заводом конструкторско-технологических мероприятий по изделию в целом и его элементам;
- выявить влияние нагрузки двигателя на его надежность по удельному эксплуатационному расходу топлива;
- сопоставить уровень надежности изделия по годам их выпуска и сравнить с уровнем надежности двигателей других марок, в том числе и с двигателями зарубежных фирм.
Исследования, проводимые по второму направлению, дают возможность:
- выявить зависимость показателей долговечности и безотказности от уровня технического обслуживания, качества применяемых масел, климатических и дорожных условий эксплуатации, квалификации водителей и ремонтников, опыта эксплуатации ит.п.;
- определить потенциальную и оптимальную работоспособность изделия до ремонта или списания, а также оптимальную периодичность и объем технического обслуживания;
- наметить предполагаемую причину возникновения отказа с проверкой вероятности гипотезы в лабораторных условиях;
- найти зависимость показателей долговечности и безотказности изделий и их составляющих элементов, используя корреляционную зависимость этих показателей от условий эксплуатации изделия, и вывести средние показатели для оценки среднего уровня надежности по стране и нормирования запасных частей. Для этого уровень надежности или ресурс двигателей по каждой эксплуатирующей организации с помощью коэффициентов корректирования приводят к эталонным условиям эксплуатации и рассчитывают среднестатистические показатели, которыми можно оперировать как средними по стране.
Вторым и завершающим этапом исследования эксплуатационной надежности изделий и их элементов является качественный анализ результатов эксплуатации. Под качественным анализом понимается сопоставление количественных показателей надежности и эксплуатационных факторов в сочетании с техническим состоянием деталей и сопряжений: состояние рабочих поверхностей, абсолютные и удельные величины износов, характер и расположение зон отказов на детали или в узле.
Выявление технического состояния и причин отказов изделия и его элементов на различных этапах наработки базируется на методах исследования их во время эксплуатации с уточнением и проверкой отдельных факторов в лабораторных условиях.
Конструктивные причины отказов
Источником получения данных для проведения качественного анализа являются специальные исследования, направленные на изучение технического состояния и выявление причин отказов изделия.
При исследовании причин отказа детали, узла или сопряжения не всегда удается выделить достоверную причину, вызванную только конструктивными, производственно-технологическими или эксплуатационными факторами.
Это обусловлено тем, что выход деталей из строя во многих случаях вызывается совокупностью одновременно действующих факторов, зависящих как от качества изготовления, так и от условий эксплуатации изделия. Поэтому при исследовании стремятся к классификации возможных причин отказов на наиболее вероятные и второстепенные, или сопутствующие, гипотетически способствующие выходу детали из строя. К разряду наиболее вероятных причин отнесены такие, исключение которых,- безусловно, могло бы устранить отказ детали или значительно продлить время её безотказной работы.
Под конструктивными причинами отказов подразумеваются такие, которые могут вызвать отказ даже при соблюдении установленных технических условий или требований другой нормативной документации на изготовление, ремонт и эксплуатацию.
К производственно-технологическим причинам отказов относятся те из них, которые обусловлены несовершенством изготовления и ремонта детали или узла.
Эксплуатационные причины отказов
Эксплуатационные причины отказов вызываются нарушением требований инструкции или установленных правил эксплуатации изделия.
В процессе длительной эксплуатации под воздействием механических и температурных нагрузок, атмосферных условий и других эксплуатационных факторов изменяется состояние отдельных деталей и узлов, постепенно уменьшается работоспособность деталей, характеризующаяся изменением их свойств вследствие износа, деформации, коррозии, эрозии, образования раковин, трещин, скопления отложений, нагара и т. п. Неизбежность постепенной утраты работоспособности и сокращения остаточного ресурса деталей положена в основу метода исследования причин отказов элементов конструкции изделий по информационным данным БАТХ. При этом эксплуатационные исследования можно разделить на три вида:
- исследования отказов и технического состояния деталей сопряжений на различных этапах наработки изделий в БАТХ отправки их на ремонтные заводы;
- исследования состояния объектов в процессе капитального ремонта на ремонтных заводах;
- исследования капитально отремонтированных изделий в эксплуатирующих и ремонтных организациях до конца установленного амортизационного срока их службы.
Наряду с перечисленными выше видами активных исследований проводятся эксплуатационные исследования новых конструктивных и технологических решений, а также методов технического обслуживания, текущего ремонта и диагностики.
Актуальность изучения оценки длительности простоя и трудовых затрат
Обобщение опыта эксплуатации дизелей ЯМЗ и автомобилей КрАЗ свидетельствует об актуальности изучения не только закономерностей отказов и выявления их причин, но также и оценки длительности простоя и трудовых затрат, необходимых для устранения отказов. В связи с этим план эксплуатационных исследований надежности изделий предусматривает накопление информации о следующих абсолютных и относительных параметрах: общем простое, вызванном отказами, удельных трудоемкостях текущих ремонтов, в человеко-часах на 1000 км и в человеко-часах на 1000 ч.
Уровень соответствующих параметров в значительной мере зависит от однородности качества деталей и узлов, что, в свою очередь, определяется совершенством технологического процесса, степенью его автоматизации, эффективностью технического контроля, уровнем организации производства.
Коллективы Ярославского объединения "Автодизель" и КрАЗ систематически совершенствуют производство в указанных направлениях, что обеспечивает снижение вероятности отказов.
Совершенствование системы технического обслуживания
Назначение планово-предупредительной системы технического обслуживания автомобиля - обеспечить его безотказность и высокий ресурс при ограниченных трудовых затратах.
Периодичность и объем технического обслуживания, устанавливаемые в результате всесторонних исследований при стендовых и дорожных испытаниях, а также во время эксплуатации, должны быть такими, чтобы сохранялась требуемая надежность автомобиля в условиях эксплуатации при различной квалификации обслуживающего персонала и применении товарных сортов масел и топлива.
В зависимости от реальных условий эксплуатации необходима дифференциация технического обслуживания. В связи с тем, что трудоемкость технического обслуживания составляет сравнительно большую долю в балансе трудозатрат на производство и эксплуатацию автомобиля, весьма актуальным является сокращение объема и выбор оптимальной периодичности технического обслуживания.
Работы, постоянно проводимые ЯМЗ и КрАЗ по снижению трудозатрат на техническое обслуживание автомобиля, составляют неотъемлемую часть исследований по повышению ресурса изделий. В комплексе, работ этого направления предусмотрено определение оптимальной периодичности отдельных операций технического обслуживания, обеспечение удобства и технологичности его проведения. Соответствующий комплекс мероприятий при одновременном совершенствовании конструкции агрегатов авто-нобиля позволил в течение 1965-1972 гг. значительно снизить трудоемкость технического обслуживания автомобиля.
С 1965 но 1972 г. в целом по двигателю трудоемкость технического обслуживания уменьшена на 34,4%.
Система технического обслуживания автомобиля совершенствуется на базе исследований, проводимых в ЭПАХ НАМИ и БАТХ заводов-изготовителей. В настоящее время назрела, очевидно, необходимость создания таких фирменных станций, чтобы техническое обслуживание автомобилей проводилось на индустриальной основе.
Информация о состоянии дизелей в эксплуатации
Информация о состоянии изделий в эксплуатации должна содержать сведения об отказах до капитального ремонта, о результатах дефектации при капитальном ремонте и об отказах между капитальными ремонтами (вторичный ресурс изделия).
Таким образом, развивается преобразование несистематизированного потока информации в управляемый.
Новые формы информации могут возникать по мере повышения ресурса изделия, а также в связи с развитием средств диагностирования состояния изделий.
Помимо информации, характеризующей качество серийной продукции, все более существенную роль начинают играть результаты эксплуатационных исследований опытных элементов конструкции, а впоследствии, по мере увеличения масштабов экспериментальных работ, будут иметь большое значение и данные статистических исследований надежности опытных образцов. Среди различных направлений развития этих исследований отметим целесообразность их форсирования, в частности, повышение нагрузочных и скоростных режимов, а также проведение пробеговых испытаний автомобилей в тяжелых дорожных условиях. Кроме того, учитывая, что трудоемкость технического обслуживания имеет большое народнохозяйственное значение, следует особое внимание обратить на испытания, связанные с оптимизацией соответствующих систем обслуживания. Вследствие многообразия факторов, от которых зависит ресурс изделия и его повышение, и усложнения задач, решаемых при доработке изделия, по мере улучшения его качества масштабы соответствующих испытаний должны систематически возрастать при постоянном повышении достоверности информации.
Виды и методика лабораторных исследований
Выше было отмечено, что эксплуатационные методы исследования надежности автомобиля и его агрегатов позволяют получить достоверную в статистическом отношении оценку соответствующей совокупности качеств.
Однако повышение надежности конструкции и совершенствование технологии изготовления сложных систем, подобных автомобилям или дизелям, должны базироваться в первую очередь на результатах конструкторских, лабораторных и расчетных исследований.
Надежность этих систем должна прогнозироваться с учетом возможности последующей доработки их по результатам эксплуатации. Объем доработки и связанных с нею экономических потерь при изготовлении и эксплуатации зависят от совершенства методов и масштабов лабораторных исследований, достоверности и оперативности расчетных исследований, сочетания расчетных и экспериментальных работ.
Усовершенствование и повышение эффективности соответствующих связей конструкторских, расчетно-теоретических и экспериментальных методов исследований надежности обусловлены использованием достижений технической физики и прикладной
математики с широким применением электронно-вычислительных машин. Естественно, что для увеличения объема и углубления исследований по повышению надежности при одновременном использовании новейших технических средств необходимо систематическое развитие лабораторной базы машиностроительных предприятий.
Остановимся на видах экспериментально-лабораторных исследований, разработанных на ЯМЗ и в определенной мере на КрАЗ по повышению ресурса продукции.
Повышение надежности деталей дизелей
Одной из особенностей исследовательских работ по надежности на данном этапе, кроме указанных выше, является их комплексный характер, обусловленный тесной связью конструкции и технологий объектов изделий массового производства, возрастающим значением технологической наследственности и наряду с этим большой зависимостью ресурса изделий от качества изготовления.
Ниже рассматриваются как конструкторские, так и технологические мероприятия по повышению надежности характерных деталей (или узлов), сгруппированные в соответствии с их предполагаемым эффектом: повышение прочности за счет:
- снижения напряжений путем конструктивных изменений;
- применения более прочных материалов;
- ограничения уровня нагрузок;
- повышения эффективности ранее разработанных и освоения новых более эффективных методов упрочнения;
- уменьшения концентрации напряжений путем применения конструктивных деконцентраторов и предотвращение концентрации напряжений, вызванной технологическими факторами;
- предотвращения или уменьшения перегрузок в процессе эксплуатации;
- уменьшения или релаксации остаточных напряжений;
- понижения динамических составляющих напряжений; снижение упругих деформаций путем:
- уменьшения концентрации напряжений;
- оптимизация конструктивной схемы силовых элементов;
- отработки сопряжений в узле;
повышение жаропрочности деталей и снижение температурных напряжений вследствие:
- ограничения или снижения температуры рабочего тела;
- повышения эффективности охлаждения;
- повышения жаропрочности или жаростойкости материала;
- совершенствования конструкции;
- уменьшение износа детален в результате:
- повышения износостойкости пар трения;
- улучшения фильтрации воздуха, масла, топлива;
- повышения эффективности уплотнения картерной полости;
- улучшения очистки деталей от технологической грязи;
- уменьшения деформации;
- повышения качества смазочных масел и топлива;
- улучшения системы смазки;
предотвращение коррозии, кавитационного и других разрушений путем:
- подбора материалов деталей;
- применения антикоррозионной защиты;
- уменьшения амплитуд вибраций вследствие снижения податливости и применения гасителей колебаний.
Совершенствование дизелей и повышение их надежности, как свидетельствует практика ЯМЗ, должны основываться на отработке рабочего процесса, снижении до минимума или предотвращении деформации, а также на исключении или уменьшении концентрации напряжений в деталях. Ниже рассмотрен опыт разработок и исследований по повышению ресурса элементов конструкций дизелей ЯМЗ (базовых деталей и ряда узлов, являющихся общими для всего семейства дизелей ЯМЗ-236, ЯМЗ-238, ЯМЗ-240 и их форсированных модификаций).
Испытания с циклическим нагружением
В процессе испытаний с циклическим нагружением при начальной амплитуде цикла, превышающей номинальную газовую нагрузку на 300%, и частоте 750 циклов в минуту амплитуды последовательно возрастают до возникновения усталостных разрушений поперечных стенок. При отсутствии разрушений через 10 ч нагрузку увеличивали ступенями на 6%, после чего цикл испытаний повторяли, и так до появления усталостных трещин.
Таким образом, вследствие оребрения поперечных стенок значительно повысилось число циклов до появления разрушения в условиях многократных перегрузок по сравнению с нагрузками, соответствующими действительному рабочему циклу.
Обобщение данных эксплуатации подконтрольных автомобилей подтвердило достаточную надежность данного элемента конструкции блока после введения описанных выше изменений.
При эксплуатации первой партии дизелей ЯМЗ были случаи недостаточной долговечности пружин клапанов системы смазки, хотя расчет на прочность показал их умеренную напряженность. Исследованиями были выявлены гидравлические колебательные процессы в системе смазки с частотой 2-1600 Гц и амплитудой 0,1-1,4 кгс/см2, а также интенсивные колебания плунжера клапанов с частотой 150-250 Гц и амплитудой 1-5 мм.
Устранение этих резонансных колебаний путем изменения массы плунжера и жесткости пружины не дало положительных результатов из-за широкого диапазона колебаний в масляной системе на различных скоростных режимах работы дизеля.
В конечном итоге требуемая работоспособность пружины была достигнута изменением конструкции клапана, в который был введен гидравлический демпфер. Использование последнего позволило создать силу сопротивления перемещению плунжера пропорционально скорости его движения и в результате демпфирования устранить резонанс.
Увеличение подачи масляного насоса со 105 до 140 л/мин значительно повысило напряженность отдельных его деталей, в особенности ведущего валика и деталей привода.
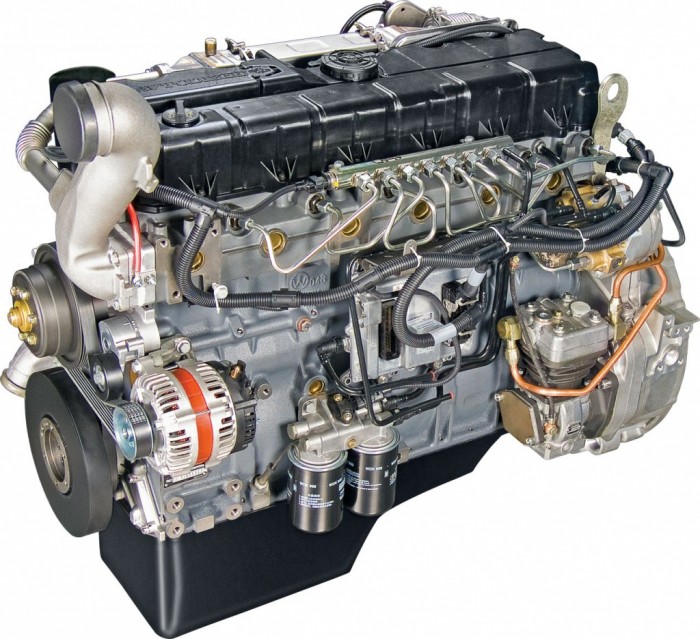
Согласно стандартной терминологии под надежностью понимается свойство автомобиля, агрегата или механизма (а в общем случае изделия) выполнять заданные функции при сохранении эксплуатационных показателей в установленных пределах в течение требуемого интервала времени или требуемой наработки (пробега автомобиля) в определенных условиях эксплуатации.
Понятие "надежность дизеля" включает его безотказность, ремонтопригодность, сохраняемость, а также долговечность его частей. Исходя из соотношения составляющих стоимости эксплуатации автомобилей, при определении их надежности следует учитывать также трудоемкость технического обслуживания, которая имеет не только экономическое значение, но и оказывает большое влияние на надежность автомобиля и особенно силового агрегата.
Эксплуатационные качества автомобилей проявляются при различном сочетании множества обстоятельств, обусловленных изменением условий эксплуатации и многообразием производственных факторов, определяемых закономерностями массового производства. При этом необходимо принимать во внимание непрерывное изменение состояния автомобилей в условиях длительной эксплуатации. Таким образом, возможно самое разнообразное сочетание перечисленных выше факторов и обстоятельств. В этих условиях качество изделий массового или крупносерийного производства является вероятностным понятием. Для воздействия на уровень их качества, другими словами, для управления им необходимо проведение соответствующих исследований во всех сферах, связанных с производством и эксплуатацией автомобилей и их агрегатов.
Все большее значение приобретают исследовательские работы в области создания и совершенствования объектов. Вследствие увеличения объема исследований, улучшения их технологии, основанного на достижениях технической физики и прикладной математики, а также усложнения комплексных производственных взаимосвязей в условиях специализации неизмеримо возрастает роль процессов, связанных с получением и использованием информации по эксплуатационным свойствам изделий, которая необходима для повышения качества автомобилей и их силовых агрегатов и в первую очередь надежности тех и других.
Естественно, что увеличение объема и углубление исследований по повышению надежности изделий, использование новейших технических средств при проведении экспериментов и анализа их результатов связаны с ростом расходов на данные работы. Эти расходы окупаются при внедрении усовершенствованных конструкций или процессов, позволяющих повысить ресурс и другие эксплуатационные качества изделий.
От уровня надежности автомобилей в большой мере зависят затраты труда и материальных средств при осуществлении транспортной работы, а также расход запасных частей и потребность в замене изделий во время эксплуатации, т. е. производственная программа предприятий-изготовителей.
Напомним, что под ресурсом понимают наработку, выраженную в километрах пробега автомобиля или часах работы двигателя до предельного состояния, оговоренного в технической документации.
После проведения капитального ремонта изделие приобретает так называемый вторичный ресурс. В настоящее время коллективы объединения "Автодизель" и Кременчугского автомобильного завода работают над тем, чтобы довести вторичный ресурс до 80% (и более) ресурса новых дизелей и автомобилей.
В процессе эксплуатации изделий возникают также отказы, устранение которых обычно требует относительно небольших затрат времени. Коллективы ЯМЗ и КрАЗ, систематически повышая безотказность изделий, подготовляют нормирование соответствующих параметров. Отказы изделий в эксплуатации и необходимость их ремонта возникают при различной наработке, что объясняется разными условиями эксплуатации, а также неоднородностью качества изделий. Для определения по совокупности полученных данных о наработке среднего или гамма-процентного ресурса, а также других показателей надежности, как, например, средней наработки на отказ и др., пользуются методами теории вероятностей. Напомним, что эти методы основаны на рассмотрении множества данных о наработке как случайных событий в их совокупности, характеризующей реальные условия эксплуатации всех автомобилей определенной модели и периода выпуска.
Соответственно главной задачей исследований надежности дизелей ЯМЗ и автомобилей КрАЗ в сфере эксплуатации является получение наиболее достоверного представления о надежности при минимальной затрате времени и материальных средств.
В настоящее время всесторонне разработаны методы выявления показателей надежности машин крупносерийного и массового производства, основанные на применении теории вероятностей. Соответствующими стандартами (ГОСТ 13377-67, 16468-70, 16503-70, 17509-72, 17510-72, 17526-72) установлена терминология, система сбора и обработки информации, планирование наблюдений, определение показателей надежности, а также требований к содержанию форм учета результатов наблюдений. На базе этих стандартов в Центральном научно-исследовательском автомобильном и автомоторном институте (НАМИ) разработаны конкретные методические указания по их применению при исследованиях надежности автомобилей.
При такой развитой системе стандартизации эксплуатационных методов исследований надежности машин целесообразно для их конкретных видов, в частности для дизелей и автомобилей, проводить специализированные методические разработки по учету особенностей изделий и условий их применения. Службы надежности Ярославского моторного и Кременчугского автомобильного заводов в основном занимаются изучением закономерностей отказов и их причин, состояния объектов в процессе разборки при ремонте, а также разработкой оптимальных методов технического обслуживания и диагностирования состояния изделий.