Цилиндро-поршневая группа
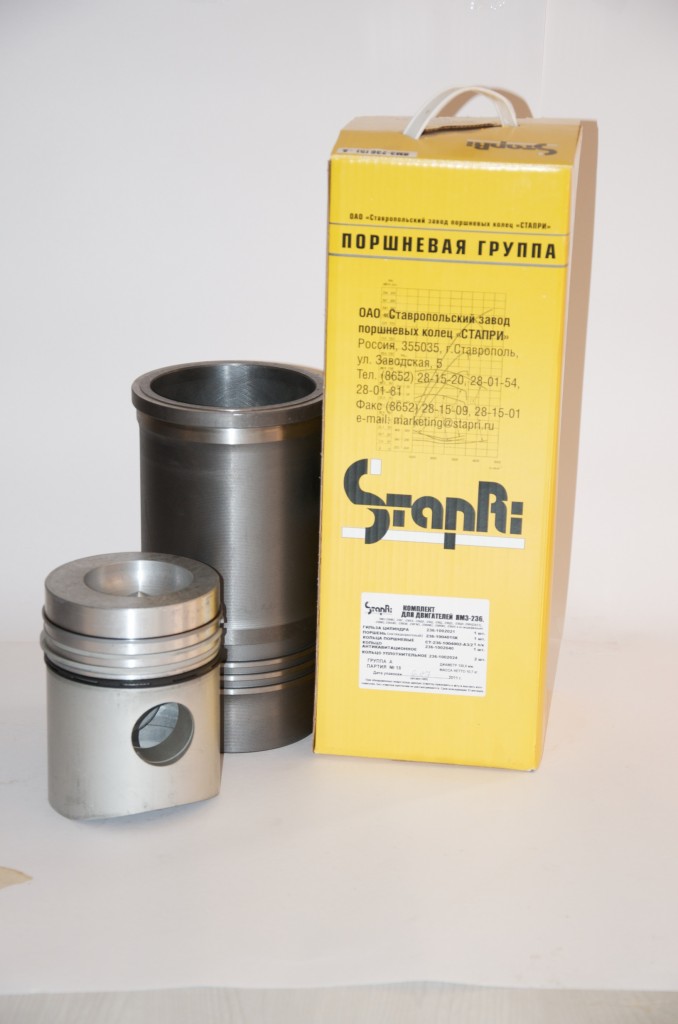
Износостойкость цилиндро-поршневой группы
Уже в начальной стадии производства дизелей ЯМЗ-236 и ЯМЗ-238 была достигнута сравнительно высокая износостойкость деталей цилиндро-поршневой группы. Увеличение ресурса двигателей потребовало дальнейшего повышения износостойкости деталей цилиндро-поршневой группы, чтобы удлинить межремонтные пробеги автомобиля.
При низком темпе радиального износа гильз цилиндров и поршневых колец в условиях эксплуатации дизелей выбор оптимального варианта конструкции деталей ограничивается чрезмерной длительностью эксплуатационных испытаний, продолжительность которых возрастает по мере повышения уровня износостойкости.
Условия работы элементов сопряжения в межремонтном интервале двигателя зависят от их исходных размеров, смазки, температуры деталей, их деформации, износа и других факторов.
Износ деталей характеризуется как максимальным отклонением размеров (например, диаметра гильз цилиндров, радиальной толщины поршневых колец) от исходных значений, так и формой эпюры износа.
Известны следующие виды разрушения поршневой группы дизеля: абразивное разрушение, коррозия, схватывание, эрозия и оплавление.
Интенсивность износа сопряженных деталей зависит от качества масла, температуры деталей, качества металла, а также характера их макро- и микрогеометрии и других факторов. Условия работы сопряженных деталей ухудшаются вследствие наличия вибраций, обусловленных динамизмом рабочего процесса и "перекладкой" поршня.
Опыт отечественного автомобильного двигателестроения свидетельствует о неоднозначной зависимости разрушения или износа деталей от действия каждого из перечисленных факторов, т. е. о необходимости учета их взаимосвязи. Поэтому возможность распространения известных концепций влияния тех или иных факторов на интенсивность износа или разрушения деталей цилиндропоршневой группы дизеля определенной конструкции подлежит комплексному изучению, результаты которого могут послужить основой методики форсированных испытаний. Вследствие этого при разработке методики форсированных испытаний деталей данной группы были выделены следующие задачи:
- обеспечение эпюры износа деталей, сходной с таковой для условий эксплуатации двигателей;
- повышение темпа износа в пределах, при которых возможна проверка заданных вариантов узла в течение ограниченного интервала времени, т. е. выбор уровня форсирования износа.
Прочность бобышек цилиндро-поршневой группы
Завершающий этап исследования прочности бобышки - оценка их прочности при работе на двигателе и прогнозирование срока службы поршня. Проведение эксплуатационных испытаний с этой целью весьма затруднено, особенно при выборе материала поршня и способа термообработки, когда необходимы сравнительные испытания нескольких вариантов.
Чтобы форсировать испытания бобышек поршня, целесообразно увеличивать напряжения в них непосредственно на работающем двигателе. Чтобы повысить максимальное давление сгорания, испытания проводят с увеличенным утлом опережения впрыска. В этом случае напряжения в бобышках возрастают в 1,5 раза. При таком увеличении напряжений нельзя ожидать резкого сокращения продолжительности испытаний, поэтому были использованы еще два способа повышения напряжений, найденные при исследовании напряжений в бобышках на специальном стенде.
Первый способ заключается в введении фаски на поверхности бобышки с внутренней стороны. В этом случае напряжения на торце бобышки возрастают в 10 раз.
Второй способ повышения напряжений-увеличение внутреннего диаметра поршневого пальца, т. е. уменьшение момента сопротивления сечения. Снижение последнего на 10% приводит к увеличению напряжений на торце бобышки в 2 раза.
По указанной методике проводятся испытания поршней на двигателе в течение 250-300 ч, выходы из строя поршней отмечаются уже через 100 ч работы, к 300 ч вероятность исправной работы поршней достигает 0,6.
Первая кольцевая перемычка является одним из наиболее нагруженных элементов поршня. Максимальные напряжения в основании перемычки возникают в момент достижения в камере сгорания максимального давления. Наиболее целесообразно оценивать прочность перемычки экспериментальным путем.