Ремонт тормозной системы автомобиля Урал
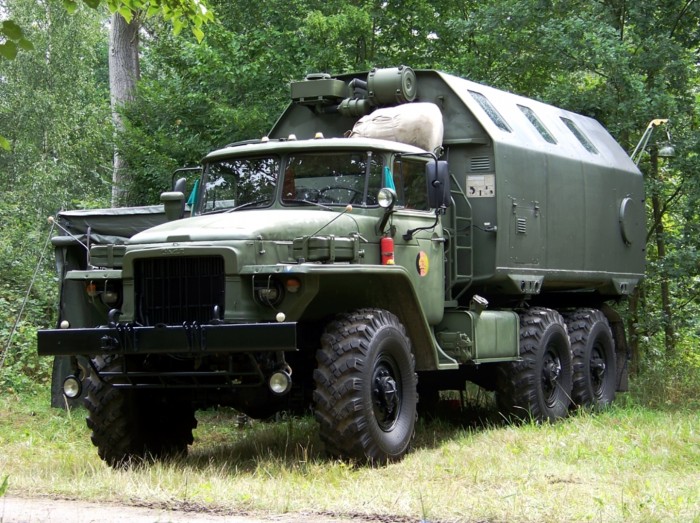
Для ремонта приборы и агрегаты тормозной системы снять с автомобиля, разобрать, промыть детали, проверить их состояние и определить пригодность деталей для дальнейшего использования.
Разборка. Разборку рабочих тормозов выполнять в следующем порядке.
Поднять мост домкратом, снять колесо и крышку ступицы, вывернуть угольник шланга подкачки шин и при помощи съемника вынуть полуось.
Отогнуть стопорную шайбу и отвернуть наружную гайку крепления подшипников ступицы, вынуть замочную шайбу и отвернуть внутреннюю гайку.
Снять ступицу с тормозным барабаном и подшипниками, стяжную пружину колодок, стопорные скобы на пальцах и колодки, очистить втулку и палец колодки.
Отвернуть трубопровод и болты, снять колесный цилиндр и разобрать его, отвернуть гайки и снять опорные пальцы колодок.
Снять щит тормоза и войлочный сальник.
Разборка пневмоусилителя, тормозного цилиндра, тормозного крана, стояночного тормоза, компрессора трудностей не представляет. При этом необходимо обратить внимание на следующее.
При разборке главного тормозного цилиндра не рекомендуется отвертывать пробку.
Головку цилиндре компрессора разбирать только при необходимости. После снят ля с помощью плоскогубцев направляющих впускных клапанов выпрессовать седла при помощи съемника.
Контроль деталей. Замасленные накладки промыть в бензине, просушить, а затем очистить рабочие поверхности металлической щеткой или наждачной бумагой. Если от поверхности накладок до головок заклепок остается менее 0,5 мм, накладки заменить новыми.
Колодки стояночного тормоза обработать совместно с разжимным кулаком, установив между сухарями колодок и кулаком пластины толщиной 0,98-1,00 мм.
Тормозные барабаны рабочего тормоза с кольцевыми канавками более 1 мм проточить.
Колесные цилиндры с рисками и следами коррозии на рабочей поверхности необходимо хонинговать. Поршни и резиновые манжеты при наличии рисок или значительном износе рабочих поверхностей заменить. Промыть и тщательно осмотреть защитный чехол колесного цилиндра, при сквозных разрывах - заменить, применяя приспособление.
Главный тормозной цилиндр. Если на зеркале главного тормозного цилиндра имеются задиры, следы коррозии, то его следует заменить или отхонинговать. При этом рекомендуется поставить новые манжеты.
При износе поршня главного цилиндра, наличии на рабочей поверхности обратного клапана и манжетов главного цилиндра следов повреждения, разбухания их необходимо заменить.
Наличие тормозной жидкости в первом цилиндре пневмоусилителя указывает на необходимость замены наружного (кольцевого) манжета поршня главного цилиндра (ослабление посадки манжета на поршне).
Пневмоусилители и детали, входящие в них, очистить и промыть. Следы коррозии и риски на рабочих поверхностях цилиндров удалить с помощью мелкой наждачной бумаги.
При наличии повреждений манжетов их необходимо заменить.
Компрессор. Корпусные детали не должны иметь трещин, сколов, а привалочные поверхности забоин и коробления. Внутренние полости должны быть очищены от отложений. Неплоскостность привалочных поверхностей корпусных деталей должна быть 0,05 мм (не более). Износ гнезд под подшипники коленчатого вала в картере компрессора допускается до диаметра 72,05 мм.
Износ впускного клапана по толщине допускается до 0,8 мм, неплоскостность клапанов - 0,01 мм. К эксплуатации допускается плунжер разгрузочного устройства с рабочим диаметром не менее 9,9 мм, а внутренний диаметр втулки плунжера -не более 10,04 мм.
Резиновые уплотнительные кольца плунжеров разгрузочного устройства не должны иметь трещин, чрезмерных износов и старения.
Непараллельность осей верхней и нижней головок шатуна допускается не более 0,07 мм на длине 100 мм.
Детали и трубопроводы тормозного привода очистить, промыть и осмотреть. При наличии повреждений детали заменить.
Особое внимание обратить на состояние и надежность крепления трубопроводов на мостах. Гибкие шланги не должны иметь трещин и потертостей.
Сборка. Сборку главного и колесных тормозных цилиндров, пневмоусилителя, стояночного и рабочего тормозов выполнять в порядке, обратном разборке. При этом необходимо обратить внимание на следующее.
Перед сборкой главного и колесных цилиндров детали промыть в спирте. Поршни, манжеты и рабочие поверхности цилиндров смазать касторовым маслом или смазкой ДТ-1. На рабочую поверхность пневмоцилиндров, штока, сальника проставки, манжетов поршней пневмоусилителей и войлочного кольца нанести смазку ЦИАТИМ-201. Болты крепления главного тормозного цилиндра поставить на уплотнительную пасту. Поршни пневмоусилителей собирать в гильзе диаметром 150 мм; устанавливают их на штоке с помощью гаек согласно размерам, приведенным на рис. 154. Гайки стяжных болтов пневмоусилителей чрезмерно не затягивать.
После сборки пневмоусилитель проверить на герметичность давлением воздуха 3,5-4 кгс/см2, при этом главный цилиндр должен создавать давление жидкости 85-100 кгс/см2. Утечки воздуха и жидкости не допускаются.
Опорные пальцы и втулки колодок рабочего тормоза смазать графитной смазкой. После сборки колесный цилиндр испытать на герметичность давлением воздуха 4-5 кгс/см2 с погружением в спирт. Утечка воздуха недопустима. При испытании должно быть исключено выпадание поршней под давлением воздуха.
После сборки рабочего тормоза при помощи опорных пальцев и регулировочных эксцентриков отрегулировать зазор между накладкой колодки и барабаном. Зазор измерять через люк в барабане щупом длиной 200 мм на расстоянии 30 мм от торца накладок. Зазор должен быть 0,35 мм в верхней части, 0,2 мм в нижней части.
При сборке стояночного тормоза разжимный кулак, втулку кулака, опорный палец колодок, а также шарнирные соединения привода (оси, втулки, пальцы) покрыть слоем смазки ЦИАТИМ-201. Все конические резьбовые соединения пневмосистемы устанавливать на уплотнительную пасту.
При сборке компрессора гайки крепления головки затягивать попарно, начиная со средней диаметрально расположенной пары, в два приема. Момент затяжки 1,2-1,7 кгс-м.
Техническое состояние компрессора проверяют на стенде при следующих условиях: частота вращения коленчатого вала компрессора 1200-1500 об/мин, давление масла, поступающего в компрессор,- 1,5-3,0 кгс/см2 и температура масла не ниже 40° С.
Производительность компрессора должна быть 220 л/мин при 2000 об/мин вала компрессора; проверяется при соединении баллона с атмосферой через калиброванный канал 0 1,6 мм длиной 3 мм. Давление в баллоне должно быть не менее 6 кгс/см2.
Одновременно проверяют маслопропускную способность. Количество масла, вытекающего через сливное отверстие в нижней крышке картера, должно быть не более 500 г за 5 мин.
Отсутствие течи масла, перегрева подшипников, посторонних стуков проверяют при работе на холостом ходу, т. е. при подаче воздуха в атмосферу. Продолжительность испытаний 5 мин.
Работу разгрузочного устройства проверяют при подаче в канал 28 (см. рис. 150) сжатого воздуха под давлением 5 кгс/см2. При этом плунжеры должны подняться и полностью открыть впускные клапаны. Одновременно проверяют герметичность уплотнения плунжеров. Падение давления за 1 мин не должно превышать 0,5 кгс/см2.
Выброс масла проверяют по масляному пятну на пластине, помещаемой на расстоянии 50 мм от торца выпускного отверстия. После 10 с работы компрессора пятно должно умещаться в круге диаметром 20 мм.
Герметичность нагнетательных клапанов проверяют по падению давления сжатого воздуха в баллоне. Падение давления воздуха в баллоне с 6-7 кгс/см2 не должно падать более чем на 0,5 кгс/см2 за 1 мин.
Сборку и регулировку тормозного крана необходимо выполнять в специализированных мастерских.