Вкладыши ЯМЗ-236, 238
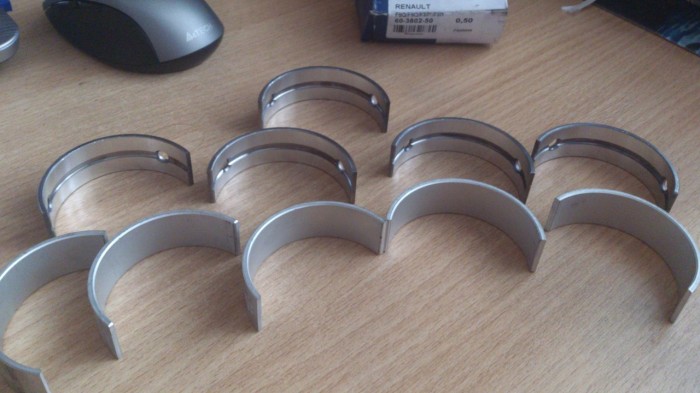
Коренные и шатунные подшипники коленчатого вала имеют вкладыши со стальным основанием, залитым свинцовистой бронзой с толщиной слоя свинцовистой бронзы после обработки 0,3 -0,65 мм. Окончательно обработанные вкладыши покрываются специальным сплавом с толщиной слоя 0,012 мм, что способствует улучшению их приработки и увеличению срока службы. Верхние и нижние вкладыши коренных подшипников не взаимозаменяемы: в верхнем вкладыше, в отличие от нижнего, имеется отверстие и кольцевая канавка на внутренней поверхности для подвода смазки.
От проворачивания и осевых перемещений вкладыши удерживаются силой трения, возникающей между вкладышами и постелями от затяжки болтов, и штампованными выступами на наружных поверхностях вкладышей, входящими в соответствующие пазы в постелях блока и нижней головки шатуна.
Для возможности ремонта коленчатого вала предусмотрены шесть ремонтных размеров вкладышей. Клеймо ремонтного размера наносится на тыльной стороне вкладыша, недалеко от стыка.
При проектировании четырехтактных дизелей ЯМЗ было предусмотрено применение шатунных и коренных вкладышей толщиной соответственно 4,0 и 5,5 мм, изготовляемых из стальной трубы. Внутренняя поверхность трубы заливалась свинцовистой бронзой. Толщина антифрикционного слоя у дизелей первых выпусков выдерживалась в пределах 0,5-0,9 мм.
Анализ данных эксплуатации показал, что усталостная прочность этих вкладышей была недостаточна, хотя расчетные нагрузки на коренные и шатунные вкладыши, определяющие их надежность, не превышают таковые у большинства современных дизелей.
Проведенные исследования позволили установить влияние толщины антифрикционного слоя на стойкость вкладышей. Испытания вкладышей с толщиной этого слоя, уменьшенной до 0,35-0,65 мм, показали, что их усталостная прочность повысилась в 1,4 раза. Дальнейшее повышение усталостной прочности было достигнуто в результате нанесения на поверхность антифрикционного слоя свинцовооловянистого сплава толщиной 0,011-0,015 мм. Уменьшение толщины бронзового антифрикционного слоя и нанесение на него указанного сплава привели к повышению усталостной прочности по сравнению с исходным вариантом в 2,1 раза. Дальнейшее уменьшение толщины антифрикционного слоя при данной технологии изготовления оказалось невозможным из-за недостаточности минимальной толщины слоя. Поэтому было освоено производство вкладышей из биметаллической тонкостенной ленты, что позволило обеспечить оптимальную толщину антифрикционного слоя.
Цикл исследований по повышению работоспособности вкладышей включал: определение расхода масла через шатунные и коренные подшипники коленчатого вала; измерение температуры вкладышей на работающем двигателе; анализ расчетных нагрузок на вкладыши; поиск путей увеличения удельных нагрузок на вкладыши с целью разработки метода форсированных испытаний; опенку износостойкости вкладышей в различных условиях эксплуатации и при различной эффективности очистки масла; оценку антифрикционных свойств различных материалов.
Определение расхода масла через подшипники
Определение расхода масла через подшипники производилось на моторном стенде с помощью специальной установки, состоящей из масляного насоса с приводом от электродвигателя и мерных баков.
Через подшипники дизеля прокачивается масло в количестве, достаточном для обеспечения гидродинамической смазки и отвода тепла от подшипников.
Последнее было проверено измерением температур вкладышей на работающем двигателе. Температура вкладышей (в зоне антифрикционного слоя) практически равна температуре масла в масляном картере двигателя. Путем расчета были определены нагрузки в функции частоты вращения коленчатого вала в зависимости от максимального давления сгорания, а также удельные нагрузки при уменьшении несущей поверхности вкладышей. Максимальные удельные нагрузки на вкладыши шатунных подшипников возникают при 1500-1900 об/мин, а на вкладыши коренных подшипников при 1900-2100 об/мин.
Один из способов увеличения удельной нагрузки на вкладыши - уменьшение их активной поверхности за счет уменьшения длины антифрикционного слоя. Так, при изменении длины вкладыша коренного подшипника с 39,5 на 20,5 мм и шатунного с 35,5 на 16,5 мм максимальная удельная нагрузка возрастает на 90% (рис. 87). После испытаний на дизеле вкладышей с уменьшенной длиной в течение 500 ч трещин и разрушений на них не было. Увеличение удельных нагрузок на вкладыши может быть достигнуто также путем повышения максимального давления сгорания. Сочетая два указанных способа повышения нагрузок, можно увеличить максимальные удельные нагрузки на шатунные вкладыши на 280-300% и на коренные на 380-400%, что целесообразно использовать при форсированных испытаниях вкладышей подшипников коленчатого вала.
Оценка вкладышей ЯМЗ
При разработке метода оценки вкладышей были сопоставлены предположительные причины их разрушения: вследствие нарушения масляной пленки при пуске, резкой перемене скоростных режимов и обкатке дизеля. Результаты испытаний, проведенных с целью проверки вероятности первых двух гипотез, не могут быть использованы для оценки антифрикционных свойств вкладышей на неустановившихся режимах работы, так как невозможно однозначно воспроизвести условия испытаний (условия подачи смазки и поддержание определенных угловых ускорений коленчатого вала).
Третья гипотеза нарушения масляной пленки не соответствует эксплуатационным условиям работы вкладышей и скорее характеризует качество изготовления подшипникового узла.
Известно, что при прочих равных условиях снижение кинематической вязкости приводит к уменьшению несущей способности масляного клина, а следовательно, и надежности подшипника. Исходя из этого, был предложен метод форсированных испытаний для сравнительной оценки антифрикционных свойств вкладышей. Сущность метода заключается в преднамеренном снижении вязкости масла в двигателе путем разбавления его Дизельным топливом. Порядок испытаний следующий:
сборка дизеля, обкатка, слив масла, заливка смеси масла с топливом в соотношении 2:1;
работа двигателя в течение 2 ч на режиме холостого хода с периодическим увеличением частоты вращения от 1700 до 2100 об мни, остановка, осмотр фильтров;
заливка смеси масла и топлива в соотношении 1:1, если в фильтрах отсутствуют частицы материала вкладышей;
работа дизеля в течение 2 ч на таком же режиме, осмотр фильтров.
После каждого осмотра в случае отсутствия частиц, свидетельствующих о задире вкладышей, в картер двигателя добавляется 10-15% топлива.
Несущую способность масляного клина оценивали по времени работы вкладышей до схватывания и вязкости смеси, используемой для смазки.
Наибольшая продолжительность испытаний одного комплекта вкладышей 10 ч.
Наибольшей усталостной прочностью антифрикционного слоя обладают вкладыши из ленты, на стальное основание которой наплавлена свинцовистая бронза, покрытая, в свою очередь, свинцовооловянистым сплавом, или освинцованная с диффузией индия. Биметаллические сталеалюминиевые вкладыши, полученные методом плакирования, имеют менее высокую усталостную прочность.
Для осуществления дальнейшего увеличения ресурса сопряжения коленчатый вал - подшипники были определены предельно допустимые зазоры в нем, при которых не происходит чрезмерного повышения напряжений в щеках коленчатого вала и падения давления в системе смазки. При увеличении диаметрального зазора в подшипниках до 0,20 мм напряжения в щеках коленчатого вала практически не повышаются. Предельно допустимый зазор в подшипниках коленчатого вала равен 0,21 мм. Вычитая из этой величины максимальный и минимальный зазоры нового двигателя, можно определить пределы суммарного износа шеек и вкладышей подшипников коленчатых валов.
По данным микрометража, после длительной эксплуатации был определен допустимый износ шеек валов и вкладышей в процессе эксплуатации с учетом промежуточной замены последних. Установлено, что при улучшении чистоты обработки поверхности шеек валов с 1/8 до 1/9 в износ их уменьшается не менее чем на 17%.
Стойкость антифрикционных материалов
Оценочным критерием стойкости антифрикционных материалов являются предельные удельные нагрузки до возникновения усталостных трещин при определенном числе циклов нагружения. В серии опытов, имевших целью выявление прочностных качеств вкладышей, было испытано несколько их вариантов. Минимальная продолжительность испытаний составила 200-300 ч.
Лучшие вкладыши работали без разрушения свыше 700 ч. Наблюдение за состоянием вкладышей в процессе форсированных испытаний осуществлялось косвенно путем периодического осмотра фильтрующих элементов масляных фильтров. При этом в систему смазки был включен щелевой фильтр - сигнализатор наличия металлических частиц в масле. Наряду с этим вкладыши периодически осматривались при разборке дизеля. Известно, что в условиях гидродинамической смазки коэффициент трения не зависит от свойств материалов подшипника и вала.
Однако в реальных условиях работы дизеля возможно кратковременное разрушение масляной пленки при его пуске, резкой перемене режимов, при остановках и в процессе обкатки, когда подшипник и вал не приработались. В этих случаях существенное значение приобретают антифрикционные свойства подшипникового сплава, которые определяются коэффициентом трения, сопротивлением сдвигу, теплопроводностью, способностью удерживать смазку и создавать оксидную пленку. Эти свойства вкладышей обычно не выявляются на дизелях при стендовых и эксплуатационных испытаниях. Выход вкладышей из строя вследствие разрушения масляной пленки носит случайный характер. Его аналитическое рассмотрение весьма затруднительно. В то же время при подборе материала вкладышей необходима сравнительная оценка их антифрикционных свойств непосредственно на работающем дизеле.